We've been investigating some intriguing Canadian E&Ps that are using this cutting-edge, yet not new, drilling technique. To make our write-ups more accessible and less tedious for those uninterested in diving into O&G theory (we know some of you fall into this category), we're introducing a new section in ZeroGCoS. It will house some technical explanations and present specialized knowledge in the most straightforward way possible. We hope you find it informative!
After this article we completed a first introductory post about the basics of hydrocarbons, in case you want to begin with it before reading this one:
Field Notes: hydrocarbons 101
Following the result of the poll, we have prepared this first article that provides basic concepts about the hydrocarbons: what they are, how the form and how they can be commercially exploited. Disclaimer: this content may not be interesting for all readers, but we aim to collect several aspects that are important to understand some technical results th…
This first technical article covers multilateral wells: the different types and why they are being more and more common in different plays and countries.
The traditional well can be considered single leg or bore and, depending on the drilling direction into the reservoir, it can be vertical or horizontal. The goal of a multilateral well is to maximise the contact area within the reservoir compared to a single-bore well, increasing the productivity and the economic return.
What’s a multilateral well
A multilateral well is a technologically advanced form of wellbore architecture. At its core, it comprises a primary wellbore called the "motherbore" from which several lateral bores—horizontal or slanted branches—extend. These laterals are designed to contact various sections of a hydrocarbon reservoir, thereby enhancing oil and gas extraction efficiency. The specific area where a lateral bore connects with the motherbore is referred to as a "junction," and the complexity of these junctions varies. Depending on the operational needs and geological considerations, junctions can range from simple open-hole connections to highly engineered, mechanically stabilised, and hydraulically isolated systems.
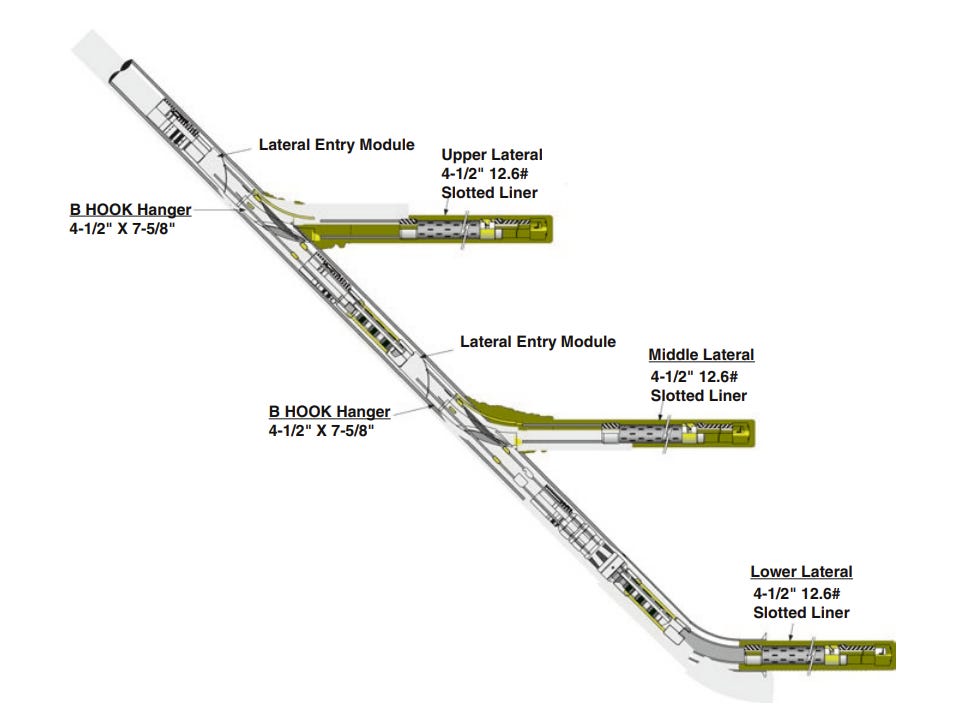
A sidetracked well is not always a multilateral
We must make the following clarification. If a wellbore is partially abandoned and a hole milled above the abandoned section to the side of the main bore, this is a sidetrack. It is a common operation when the original wellbore is no longer usable, but there are nearby reserves and is usually considerably cheaper than drilling a new well. If the original wellbore is not abandoned, but only temporarily isolated and a sidetrack drilled, production or injection from both the sidetrack and original wellbore can be achieved, then we have a multilateral.
The different sections
Operators began employing basic forms of Multilateral (ML) wells as far back as the 1950s. By 1997, the increased variety in ML well configurations led to the formation of a consortium called Technology Advancement of Multilaterals (TAML). Comprising both operators and service companies, this group developed a standardized classification system for ML wells based on the type of junction connecting the main bore to the lateral, not on the whole well design. This system resulted in the creation of TAML Levels 1 through 6, each detailing different complexities and functionalities of the well junctions.
Every ML doesn’t need to incorporate these 6 TAMLs, and the number of TAMLs used will depend on the geology and the characteristics of the reservoir. Each TAML requires specific completion techniques, which will be designed before beginning the drilling. The data collected while drilling can also be used to refine the design and optimise the completion of the ML well.
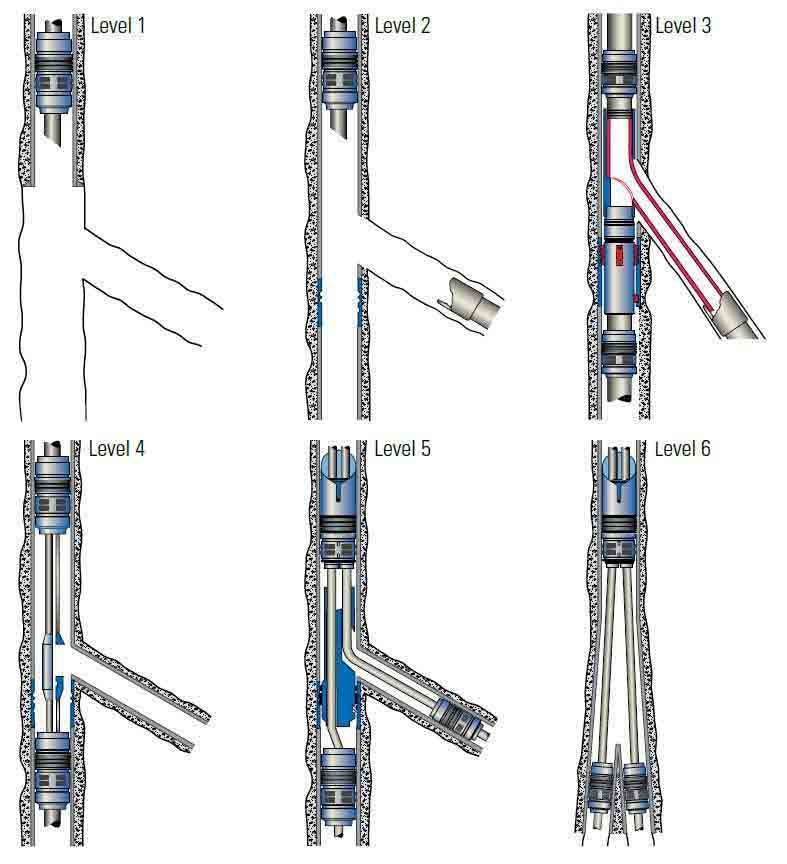
TAML Level 1
This is the most basic and straightforward type of multilateral well, and it's best used in hard rock formations that are naturally strong. Since it's just a simple hole without any extra casing or liners, it's pretty cheap to drill. However, this simplicity comes with trade-offs. For one, it's tough to go back into the well to make any changes or repairs later on. Additionally, because there's no pressure control at the point where the well branches off, you have to be cautious about changes in pressure or unwanted mixing of fluids between the branches. Some people add slotted liners in the branches for a bit of extra strength, but that doesn't fully solve the issues with pressure and the risk of things like sand getting in.
TAML Level 2
This is a step up from the basic Level 1 design. The main difference is that the main hole gets a casing, which is like adding a protective sleeve, making the whole structure more stable. You also have the option to add liners to the side branches to make them a bit stronger, especially if the rock there isn't as hard. It's going to cost you more in both time and money compared to Level 1, but the upside is that you can drill multiple branches off the main hole and have a bit of wiggle room to fix issues later. The catch is that you still don't have a way to fully control pressure where the branches connect to the main hole.
TAML Level 3
In this design, both the main hole and the side branches get a casing, but only the main hole is cemented for additional strength. This option takes even more time and money than Level 2 but offers you a lot more stability and flexibility. For instance, if issues pop up later—like unwanted water or gas—you have some ability to go back in and address them. The well is better suited for a wider variety of rock types. However, even with these improvements, you still can't manage pressure perfectly at the point where the well branches off.
TAML Level 4
This design is for the tougher cases, like when you're dealing with loose or unstable rock. Both the main hole and the side branches are cased and cemented, which is like adding a really strong protective layer. This makes the well super stable. Plus, you can use devices called packers to separate production between the main hole and the branches. For example, if one branch starts producing too much water, you can effectively 'shut it off.' But all these features come at a price—it takes more time to drill, and it's more expensive. You also need a wider hole to fit all this stuff, which adds to the cost.
TAML Level 5
This is where things get really advanced. The big win here is that you get full pressure control at the junction where the well branches off, thanks to specialized equipment like tubing strings and packers. This allows you to produce oil or gas from both the main hole and the branches at the same time, even if the rock is loose or crumbly. However, this design is complex and requires a lot of precision, which means it's also the most expensive so far. The larger hole size needed for all the equipment can also lead to more potential issues down the line, like equipment failures.
TAML Level 6
This is the top-of-the-line, most complex design out there, aimed at very weak and unstable rock formations. It uses specially made junctions that are installed deep in the well to help control pressure. This gives you a strong base to extend the branches through even the most fragile rock. You have a lot of flexibility—you can isolate or combine production from different branches and either produce or inject fluids independently. But all this flexibility and control come with a hefty price tag. The well takes the longest to drill, costs the most, and has the highest risk of mechanical issues because of all the complex parts involved.
The benefits
One useful metric for determining the applicability of multilateral wells is by comparing their value against that of traditional single-bore wells based on the same overall exposure to the formation. This quantitative approach aids in gauging the economic viability of a multilateral setup. It's essential to note that multilateral wells often require fewer feet to be drilled, translating into saved rig time.
One of the primary differences between multilateral and conventional horizontal wells is the level of complexity. Horizontal wells involve a single, usually long, horizontal section that targets a specific layer or zone of the reservoir. In contrast, multilateral wells can make simultaneous contact with multiple zones or layers, thus maximizing the reservoir contact area. This often results in increased production rates and offers superior reservoir management capabilities.
It's worth mentioning that multilateral well technology is often employed in Steam-Assisted Gravity Drainage (SAGD) applications, particularly for heavy oil reservoirs. Here, horizontal well pairs are constructed closely to facilitate the injection of steam into the formation, thereby lowering the hydrocarbon viscosity and enabling conventional drainage.
In terms of advantages, multilateral wells have the potential to significantly enhance hydrocarbon recovery. Over a longer time horizon, they may prove to be more cost-effective per lateral, even though the initial investment is higher. The capacity to selectively produce or isolate specific reservoir zones offers additional operational flexibility. Also, by requiring fewer surface wellheads, multilateral wells reduce the environmental impact, which is an increasingly important consideration in today's regulatory landscape.
Not all are the same
As we commented before, ML wells can have different configurations that depend on the characteristics of the target reservoir (and the budget in some cases). Hence, there are different ML wells depending on the configuration chosen.
For example, if the E&Ps drill what are called “open hole multilaterals“ (TAML 1), the drilling is made even less expensive, as the costs associated with running, cementing, and perforating the casing are eliminated. In open hole completions, the production zone is left uncased, allowing oil or gas to flow from the formation into the wellbore. This can offer advantages in terms of maximizing IRRs, but it may also pose challenges in terms of well control and formation stability as we saw ealier.
The picture below shoes the different completion that can be applied to the legs of a ML well.
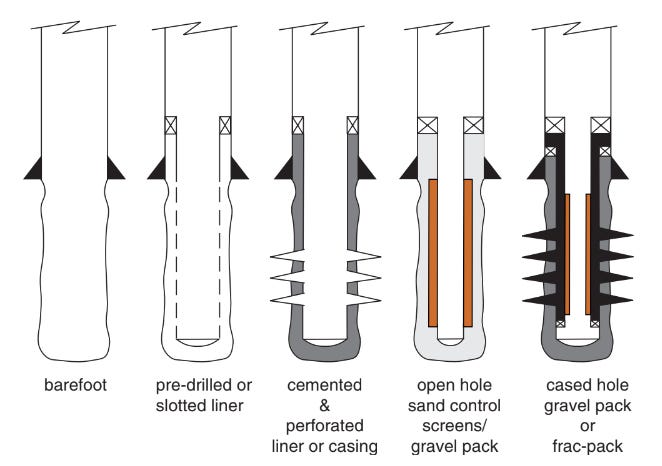
Geometry
The ML wells can be drilled using different patrons, which will are selected to optimise production from the reservoir. The petroleum engineers together with the geologiest will decide what geometry and completion is the most efficient to maximise the production and IRR.
Below we show some examples, and the selection will depend on the presence of one or multiple reservoirs, the width of the reservoirs or the porosity/permeability of the reservoirs.
Octozonals
Staggered
Stacked
Fishbone
And that’s all. We are investigating some Canadian E&Ps that use multilateral wells in some way or another. We will write soon at least about one of them. Subscribe so you don’t miss that.
Great job!
Amazing job!!